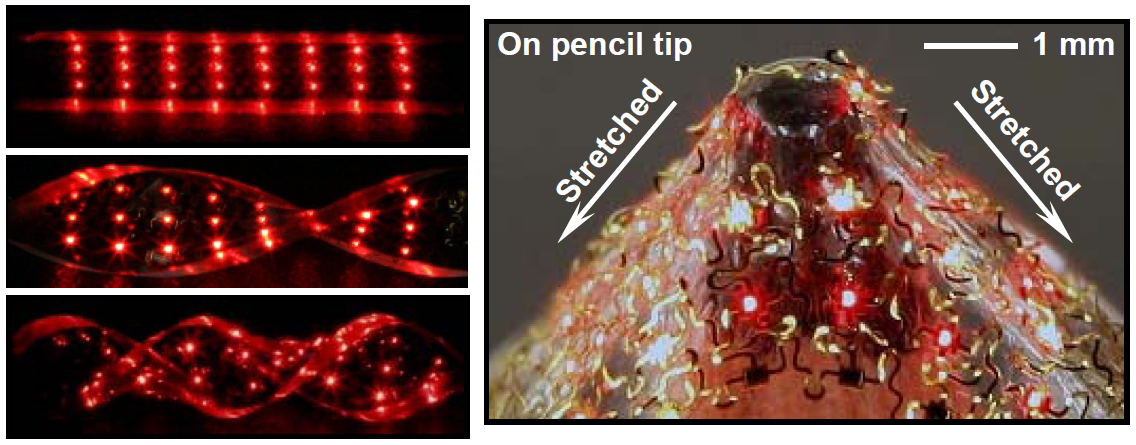
Stretchable electronic arrays. The LED sheets can be twisted by 720 degrees and considerably stretched. The wavy metal wires are visible in the image on the on the right. Reprinted by permission from Macmillan Publishers Ltd. Nature Materials (2010). doi:10.1038/nmat2879
Take a piece of silicon, try to bend it and it will break. Stretch a thin film of gold and it will rupture. Conventional metals and semiconductors are brittle and not elastic at all. But these are properties that you need when you want to use electronic devices in unusual places and for unusual applications. In biomedicine for example, if you want to put a diagnostic sensor on top of a muscle. In electronics, when you want to put a large-scale solar cell on the curved top surface of a car.
Sure, you can make a thin film and warp it around a cylinder, and if you do this with electronic circuits it is called flexible electronics. Organic electronics and very thin metal films on plastic can do this. But you cannot fit a two-dimensional sheet on a sphere without stretching it. For such applications you need what is called stretchable electronics, which is different to the flexible electronics that has been around for a while.
The latest milestone has been achieved by John Rogers and colleagues from the University of Illinois in Urbana-Champaign. They demonstrate (disclaimer: in my journal, Nature Materials) a fully biocompatible and implantable stretchable structure containing large arrays of light-emitting diodes and photodetectors. The sheets are stretchable and can be twisted by more than 720 degrees without damage, and can be brought into almost any desirable shape or configuration, says Rogers. “This advance suggests a technology that can complement features available with organic light emitting diodes, where peak brightness and lifetime are limited, and conventional inorganic LEDs, where relatively thick, brittle supports restrict the way that they can be integrated together and the substrates that can be used.”
Takao Someya from the University of Tokyo, who works on large-area organic electronic devices, highlights in particular applications in biomedicine. “Achieving biocompatibility in photonic devices that can be integrated together with soft microfluidic devices, tubes, and related platforms will play an important role in clinical medicine. In addition, although the present device relies on a single color of light, other wavelengths could be made available, in principle, by using different kinds of semiconductors.”
To fabricate the stretchable structures, Rogers and his large group of coworkers rely on a technique for stretchable electronic elements they have demonstrated before. They use metallic wires on a stretchable organic substrate (PDMS) that have many bends so that they can stretch out under tension. The LEDs themselves are made from a conventional red light-emitting semiconductor, but they are tiny, in the micrometre range, so they can conform to the bending and the stretching of the sheets.
The electronic sheets containing all this wiring and LEDs are rather complex and are made from multiple layers put on top of each other. The assembly of the electronic components happens not on PDMS but on a more suitable substrate, glass coated with PMMA. The finished sheets are then transferred in a rubber-stamp like printing process onto the flexible PDMS. Even multiple layers of LEDs are possible. Rogers has commercialized this kind of printing technique with a number of companies that exploit it for stretchable solar cells, electronic devices, bioimplants and so on. They are then coated with epoxy and another PDMS layer on top to encapsulate the electronics and to make it biocompatible, although whether these systems have long-term biocompatibility on the order of years is not clear yet.
As to the light-emitting sheets, these can be easily twisted by 720 degrees without any loss of function, and can be picked up and stretched by sharp objects like a pencil tip. Furthermore, says Rogers, their systems operate “when completely immersed in water and biofluids, thereby opening up application possibilities in biotechnology and clinical medicine.”

Position sensors on a surgical glove. The arrows point to the light-emitting (left) and photodetector part (right) of the position sensing array. Reprinted by permission from Macmillan Publishers Ltd. Nature Materials (2010). doi:10.1038/nmat2879
As an example, they implant a thin sheet under the skin of mice. The LEDs remain visible and functioning as “LED tattoos”. This suggests uses in medical diagnostics. Furthermore, the scientists incorporate a LED sheet into surgical gloves or on robotic systems. There, a combination of LEDs and photodetectors can be used as a proximity sensor, because the light that is reflected back from the scanned surface decreases as a function of distance.
As for commercial applications, cost might be an issue says Someya, and there could be a trade-off between performance and price. “In general, silicon-based large-area electronics is expensive. In contrast, organic electronics will be cheap, while electronic performance is not sufficiently high. Some implantable high-end electronics will be realized by silicon-based electronics; however, there are many important applications like wearable health-monitoring, which requires very cheap commodities that can be realized by organic electronics.”
In any case, now that even miniature optoelectronic components haven been demonstrated stretchable electronics appears to enter the realm where almost all desirable functionality is available for curved surfaces and in a broad range of application scenarios, ranging from wearable electronics to bioimplants. The limit in this area seems no longer the functionality of what can be done, but solely the creativity of those wanting to make use of stretchable electronics.
Reference:
Kim, R., Kim, D., Xiao, J., Kim, B., Park, S., Panilaitis, B., Ghaffari, R., Yao, J., Li, M., Liu, Z., Malyarchuk, V., Kim, D., Le, A., Nuzzo, R., Kaplan, D., Omenetto, F., Huang, Y., Kang, Z., & Rogers, J. (2010). Waterproof AlInGaP optoelectronics on stretchable substrates with applications in biomedicine and robotics Nature Materials DOI: 10.1038/nmat2879
Trackbacks/Pingbacks
[…] This post was mentioned on Twitter by Joerg Heber, Lucy Rogers. Lucy Rogers said: RT @joergheber: Stretchable “LED tattoos” under your skin. More likely for diagnostics than for show-off. http://wp.me/p10L8F-fC (/ @andysc) […]
[…] I’ve got you under my skin – [blog.joerg.heber.name] Take a piece of silicon, try to bend it and it will break. Stretch a thin film of gold and it will rupture. Conventional metals and semiconductors are brittle and not elastic at all. But these are properties that you need when you want to use electronic devices in unusual places and for unusual applications. In biomedicine for example, if you want to put a diagnostic sensor on top of a muscle. In electronics, when you want to put a large-scale solar cell on the curved top surface of a car. […]
[…] are one of the pioneers in this area. In this work, they make ‘LED tattoos’, tiny light-emitting diodes and photodetectors embedded into a stretchable substrate that could be im…. Other uses of stretchable electronic devices include implants to monitor heart or brain […]